Revealing Skeleton Clocks
By Mark Frank Posted August 2012
|
|
When most people think of an antique clock, they see an image, perhaps of a wooden-cased grandfather-style clock, or one of the many black slate mantle clocks that adorned the homes of many of our parents and grandparents. However, there was a small subset of antique clocks that were designed to be seen without an external case in order to display the movement as completely as possible. It would not be sufficient to simply pull an ordinary movement from its case and display it under a glass dome. Conventional movements have their wheels between two solid plates, not much to look at. So to make the clock visually interesting, the plates themselves are cut out, sometimes referred to as "fretting," to allow one to see through the plates and further reveal the clockwork within. When this is done for the sake of the clock movement itself being seen without any external conventional case, it is called a “skeleton clock,” and the clock plates are referred to as "frames."
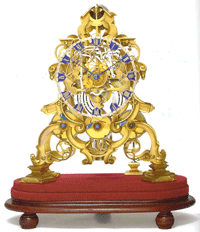
|
Photo 1: John Bennet, England, c. 1870, thick (7/8 inch), massive gilded,
cast-brass plates with deep scrollwork carving, polished edges and interior
stippling, 24 inches, 75 lbs.
|
Often, this fretwork took on fanciful
designs, from the organic and curvilinear
ivy leaf to the angular architectural styles
based on famous public buildings or
churches. Usually, the focus of the clock is
on the fretted frames. These could become
so elaborate as to nearly obliterate the
wheels’ works between them, to almost
the same degree as would conventional
solid plates (photo 1). On rare occasions,
the frames were minimized and their
design pushed into the background as far
as possible to allow the wheelworks to
come to the fore (photo 2). Sometimes, the
balance between frame and wheelworks
were completely harmonized (photo
3). There are even completely unusual
mechanisms where the clock is only a
part of a larger structure (photo 4). Others
have used unusual materials like cut rock
crystal for the wheel hubs (photo 5).
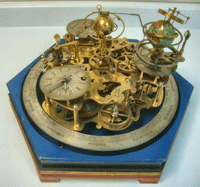
|
Photo 4: Unknown maker, England, c. 1890; an orrery containing numerous
celestial indications and continuously driven by a detent chronometer clock,
14 inches in diameter.
|
Aside from the very early domestic iron
clocks of the 15th century and the English
lantern clocks that followed in the late 17th
and into the 18th centuries which showed
the internal movement simply to save on
materials, the fi rst true skeleton clocks
created solely for the purpose of displaying
the internal mechanism began in France in
the mid 1700s. It wasn’t until the Industrial
Revolution was in full fl ower during the Victorian Era from roughly 1830 through
1900 that the skeleton clock became
widely popular, especially in England.
Several manufactories, largely located
in the Clerkenwell area of London,
produced a great many varieties of
skeleton clocks to fi t all manner of
household budgets of the day. The newly
introduced machine tools allowed for the
semi-automated process of making what would otherwise be a very time-consuming
and expensive product if made entirely
by pre-industrial methods. The people
who bought them looked upon these as
examples of the Modern Era’s industrial
prowess, similar to the other mechanical
marvel of the day, the steam engine.
For the more upscale, expensive and
complex skeleton clocks, the customer
could order their clock with all manner
of “options” from a retailer’s catalog, not
unlike the way one orders an automobile
today from the dealer’s showroom fl oor.
For example, one could have silvered
appliqués adorn the frame. The various
components holding the wheels and fl y
fans could either be cutout out from a solid
form or have that same part also fretted
within the interior of the part (photo 6).
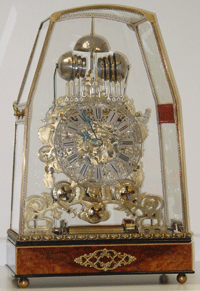
|
Photo 6: Smith of Clerkenwell,
England, c. 1850, ivy leaf design.
Complex quarter-striking clock
with four-tune music box tripped
automatically six times per day.
|
The other major country to produce
skeleton clocks at the time was France.
There, things were quite different. The
general public did not take such a great
fancy to skeleton clocks as did their
counterparts in England, and so, the
production was far less prolifi c and aimed
at a more exclusive clientele. The quality
and materials were generally better than
in England and further refl ected what
one might have expected in the Pre-
Industrial Era. These clocks were also
adorned, as is often the custom in French
clocks, with elaborate enamel dialing
and ormolu embellishments which also
added to their cost. French skeleton clocks are highly valued today, (photo 7).
For many years, skeleton clocks were
largely shunned within the horological
community. It was not until F.B. Royer-
Collard published his Skeleton Clocks1 in
1969 to be later followed on by two books2
by Derek Roberts in 1987 and 1989 that
collectors began to take notice of these
masterpieces of the art of clock making.
Today, they are much sought after, and those
examples that have rare complications
(special features or functions, such as
calendars, moon phases or astronomical
functions) or display extreme skills
in the presentation of the frame, dial
or wheelworks command premium
prices, some into the six-figure range.
In the Modern Era, there are still people
who try their hand at demonstrating their
skills at making a beautiful skeleton
clock. One of the more complex skeleton
clocks made in the 20th century was
done by a country clockmaker, Paul
Pouvillon, in France from 1918 to1939,
(photo 8). For the 21st century, I have
commissioned a complex astronomical
clock that has more than 350 wheels, 20
complications and is designed to entertain
the viewer with an ever-changing range
of movements throughout the mechanism
(photo 9). It will be one of the most
complex clocks made. One can follow the
construction in real time at http://www.my-time-machines.net/astro_index.htm.
As with any other popular type of
antique, one needs to guard against fakes.
There are a great many modern copies of
classic skeleton clocks coming currently
from China, and there are a number of
reputable fi rms who sell these as what they
are: modern, low-priced and attractive
decorative pieces. Over the years, the
Chinese copies have become better, and
unfortunately, unscrupulous resellers,
especially within online venues like eBay, advertise these as antique. I’ve even seen some mainstream
auctioneers who have “unknowingly” sold these as genuine
antiques. Selling copies as authentic or antique is inexcusable
as a careful look at the brass frames should show signs of the
small casting fl aws that were present in any cast frames made
prior to the 1920s. Modern brass is mill-rolled and contains no
such imperfections. Other signs to look for are a lack of wear
on the pinions, dial surfaces and especially the screw heads.
Any clock over 100 years old has probably been taken apart
at least a few times for servicing, and the slots on the screw
heads should show at least some distress from prior repairers.
This is especially true if the screws have a blued fi nish.
Finally, if the price seems too good to be true, it probably is!
----------------------
1 F.B. Royer-Collard, Skeleton Clocks, (N.A.G. Press Ltd., London, 1981)
2 Derek Roberts, British Skeleton Clocks, (Antique Collector’s Club Ltd., Suffolk, 1987)
3 Derek Roberts, Continental and American Skeleton Clocks, (Schiffer Publishing Ltd., USA, 1989
Mark Frank has been a collector of clocks for the past 20 years. His focus is on the theme of those clocks where one can readily view the mechanism. Skeleton clocks achieve this goal; tower clocks do the same on a much larger scale. He also restores and repairs clocks and tower clocks for his collection, and he engages in public speaking and writing on antique clocks. In 1983, he teamed up with Buchanan of Australia to create a complex fantasy clock mechanism that is due for completion in 2014 and will be one of the most complex clocks ever created. You can see some of his collection and contact the author through his website at: www.my-time-machines.net
.
All clocks, except 1 and 13, are from the author’s collection. Height measurement is the clock without a dome.
|
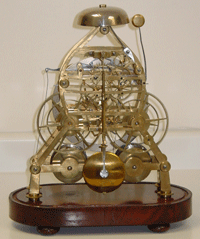
Photo 2: Samuel B. Gaze, England, c. 1830, 13 inches high.
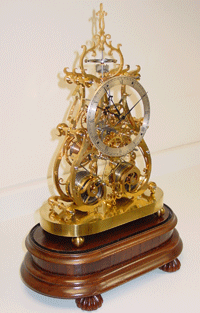
Photo 3: James Condliff, England, c. 1860, 17 inches high. A replica of it has been made by J. Zygowski.
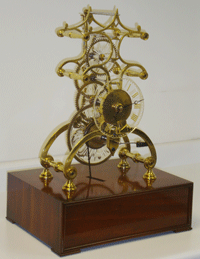
Photo 5: James Edwards, England,
c. 1840, cut crystal wheel hubs,
16 inches high.
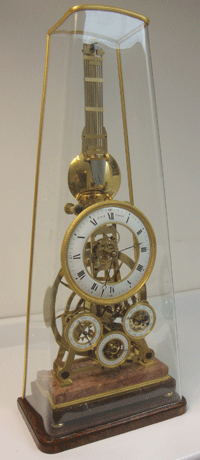
Photo 7: Henry Lepaute, France, c. 1830, inverted
pendulum design with day, date and month calendar,
29 inches high.
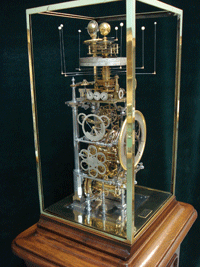
Photo 8: Paul Pouvillon, France, c. 1930, an
extraordinary astronomical clock with more
than 44 various indications. Considered the most
complicated clock built for its size, 20 inches high.
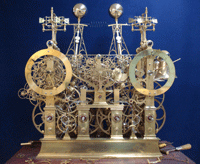
Photo 9: Modern skeleton clock by Buchanan of Australia, currently under construction. Custom-built to the author’s design with more than 350 wheels and 8,000 parts. Created to visually mesmerize through the use of movement and complications.
|